The differences between technical tubes made of polyurethane, polyamide, and polyethylene are crucial when designing an installation: they directly affect performance, durability, and compatibility with the working environment. Each material has its strengths and limitations, and knowing them is key to choosing the right solution for any pneumatic or industrial fluid system.
In this technical guide, we compare their most relevant properties based on real performance data.
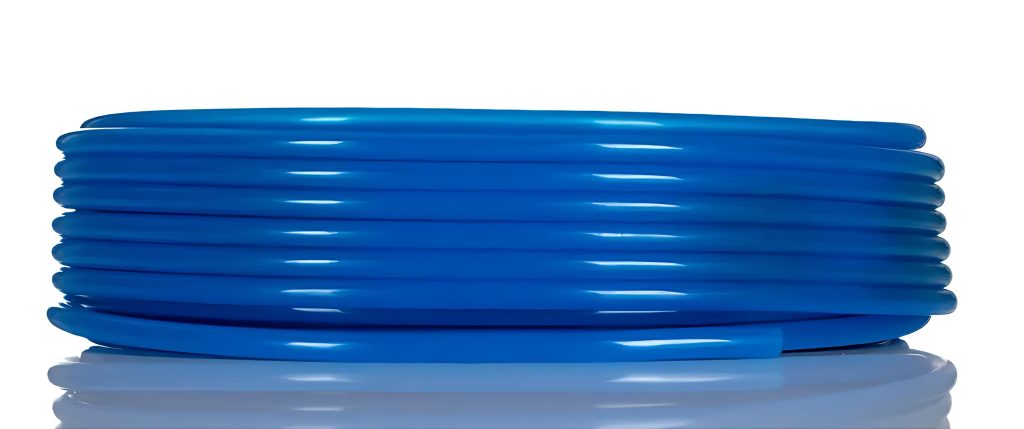
General Technical Properties
Composition and Structure
- Polyurethane (PU): Polyester or polyether base depending on the application. Known for its flexibility and good mechanical strength.
- Polyamide (PA): Manufactured according to DIN 74234, usually PA12. Excellent performance under mechanical stress and vibrations.
- Polyethylene (PE): Thermoplastic with high chemical compatibility. Suitable for food contact.
Operating Temperature Range
- PU: from 0ºC to +60ºC
- PA: from -35ºC to +100ºC (peaks up to 120ºC)
- PE: from -29ºC to +66ºC
Working and Burst Pressure
- PU: Ideal for standard pneumatic applications. Its pressure resistance varies depending on the tube diameter, but offers a good balance between flexibility and the ability to handle compressed air. Always check the manufacturer’s tables for proper use.
- PA: A very robust option. Can withstand up to three times its working pressure without bursting, making it perfect for systems with pressure spikes, such as hydraulic installations or demanding air lines.
- PE: Designed for moderate pressure, typical of water or misting applications. Not the most pressure-resistant option, but sufficient where chemical compatibility and food safety are priorities.
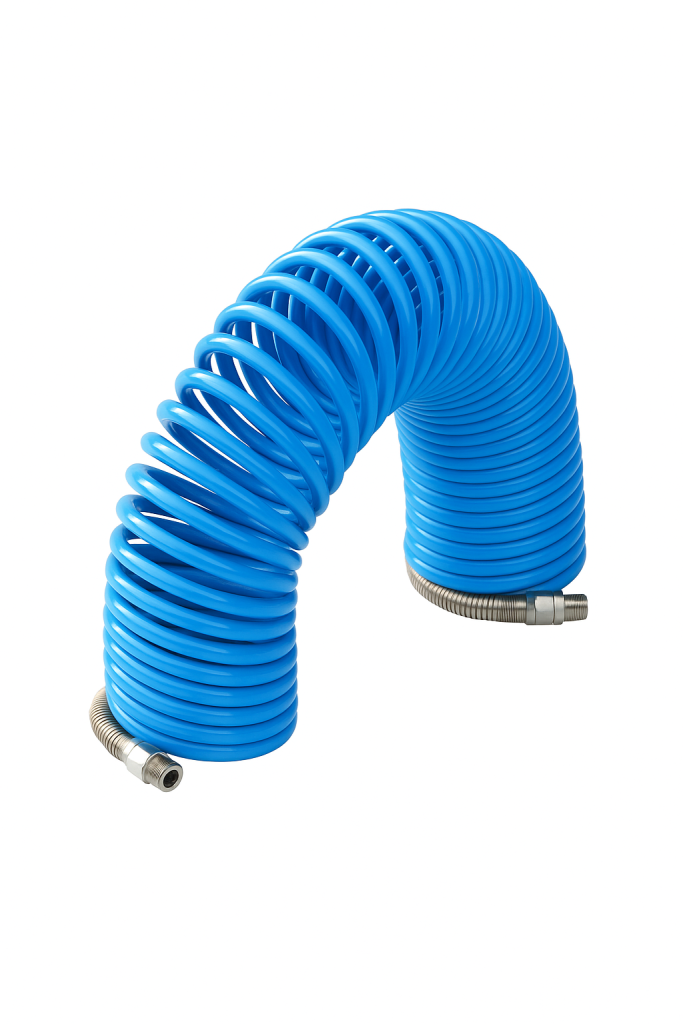
Chemical and Mechanical Resistance
Resistance to Chemicals and Harsh Environments
- PU: Good abrasion and mechanical wear resistance. However, it may degrade with prolonged exposure to water, steam, or aggressive chemicals. Recommended for dry and controlled environments.
- PA: Excellent performance against oils, fuels, solvents, and industrial chemicals. Its ability to work in demanding conditions makes it ideal for automotive and hydraulic applications.
- PE: High chemical resistance, especially against acids, alkalis, and cleaning agents. Preferred in hygiene-sensitive environments such as food, pharmaceuticals, or potable water systems.
Mechanical Resistance, Impact, and Fatigue
- PU: Good impact resistance and performance under repetitive stress. Ideal for dynamic systems with constant movement or handling.
- PA: High mechanical strength. Handles vibrations, tension, and demanding conditions without deforming. One of the most durable materials for technical applications.
- PE: Adequate mechanical performance in static or low-demand applications. Not recommended for systems with continuous mechanical stress or frequent impact but suitable for fixed, secure installations.
Flexibility and Bending Radius
- PU: Excellent. Suitable for continuous movement, coiling, compact systems, or robotics. Maintains its shape without collapsing.
- PA: Less flexible, but good buckling resistance and high dimensional stability.
- PE: Medium flexibility. Can bend over wide radii, but avoid tight curves to preserve integrity.
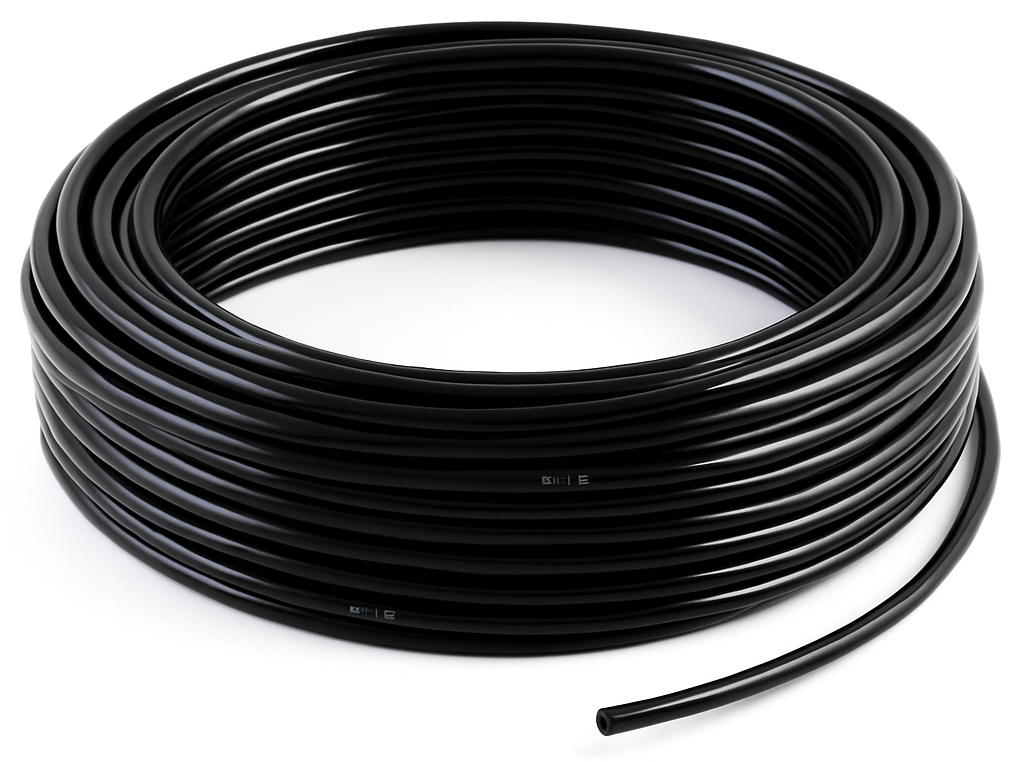
When to Use Each Tube
Polyurethane (PU)
- Compressed air and vacuum systems
- Recommended for use with automatic fittings
- Not suitable for water
Polyamide (PA)
- Water, pneumatics, gases, oils, and hydrocarbons
- Versatile use between air and fluids
Polyethylene (PE)
- Purified water and misting systems
- Ice and water machines
- Suitable for food contact when certified (FDA, EC1935)
How to Choose the Right Tube: Key Differences Between Technical Tubes
These three materials are among the most common in the industry. As always, the choice depends on the fluid, environment, and specific application.
- Polyurethane is ideal for pneumatic applications (compressed air and vacuum). Its flexibility and lower cost make it perfect for such uses. It should not be used with water.
- Polyamide may not be the first choice for air-only applications (less flexible and more expensive), but it’s much more versatile: suitable for oils, hydrocarbons, and water. It also offers high chemical and mechanical resistance.
- Polyethylene, thanks to its resistance to chemicals and cleaning agents, is the go-to option for food contact or hygienic applications—provided it’s certified. For these environments, always use a reliable and certified supplier.
While we focused on PU, PA, and PE here, the world of industrial tubing includes many other materials like PTFE (Teflon), rubber hoses, and reinforced tubing. Choosing the right one requires technical knowledge and sector experience. If in doubt, don’t hesitate to contact us — we’ll help you find the right solution for your installation.
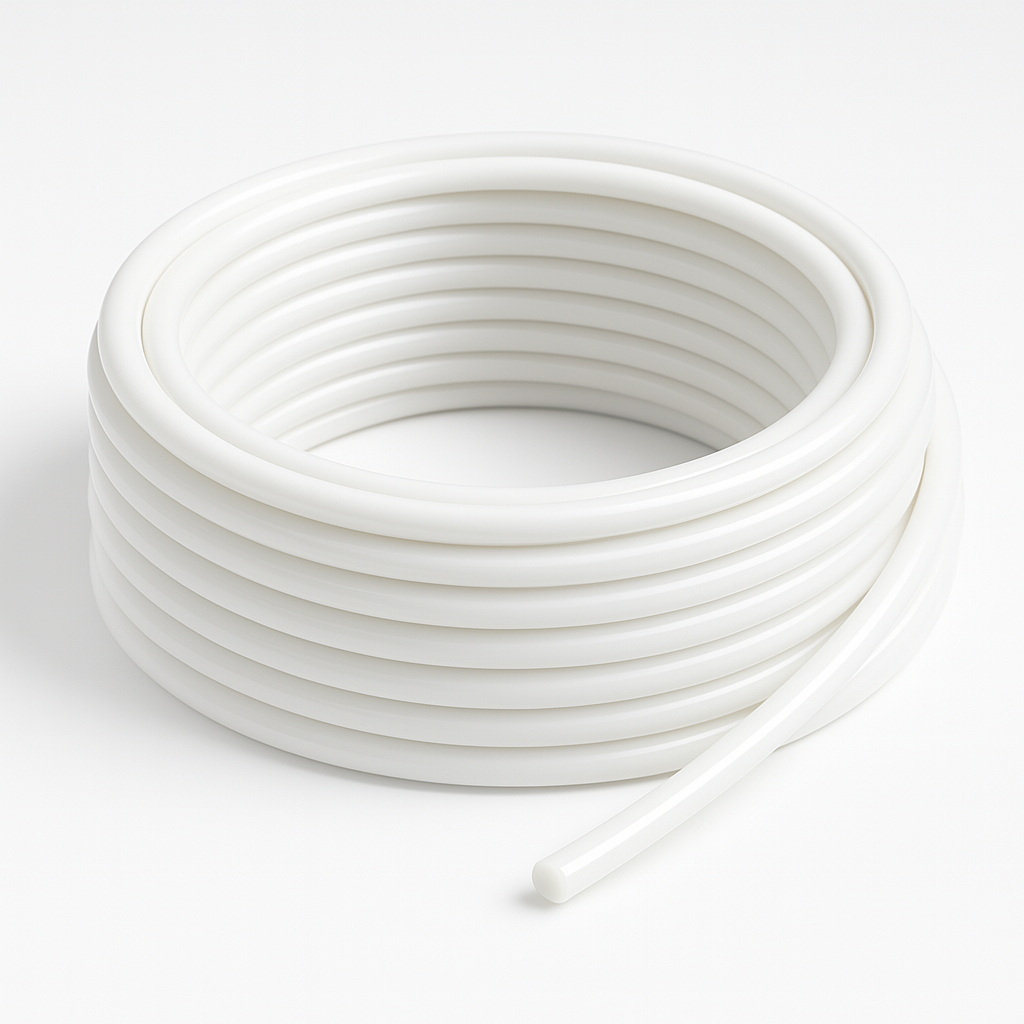
Conclusion
We’ve analyzed the main differences between PU, PA, and PE technical tubes. But there’s a vast range of tubing types waiting to be discovered. Follow us on LinkedIn for more updates, products, and applications.